Prop Tarantula Leg Connector Component Development
Problems with Original System
Concept Ideation
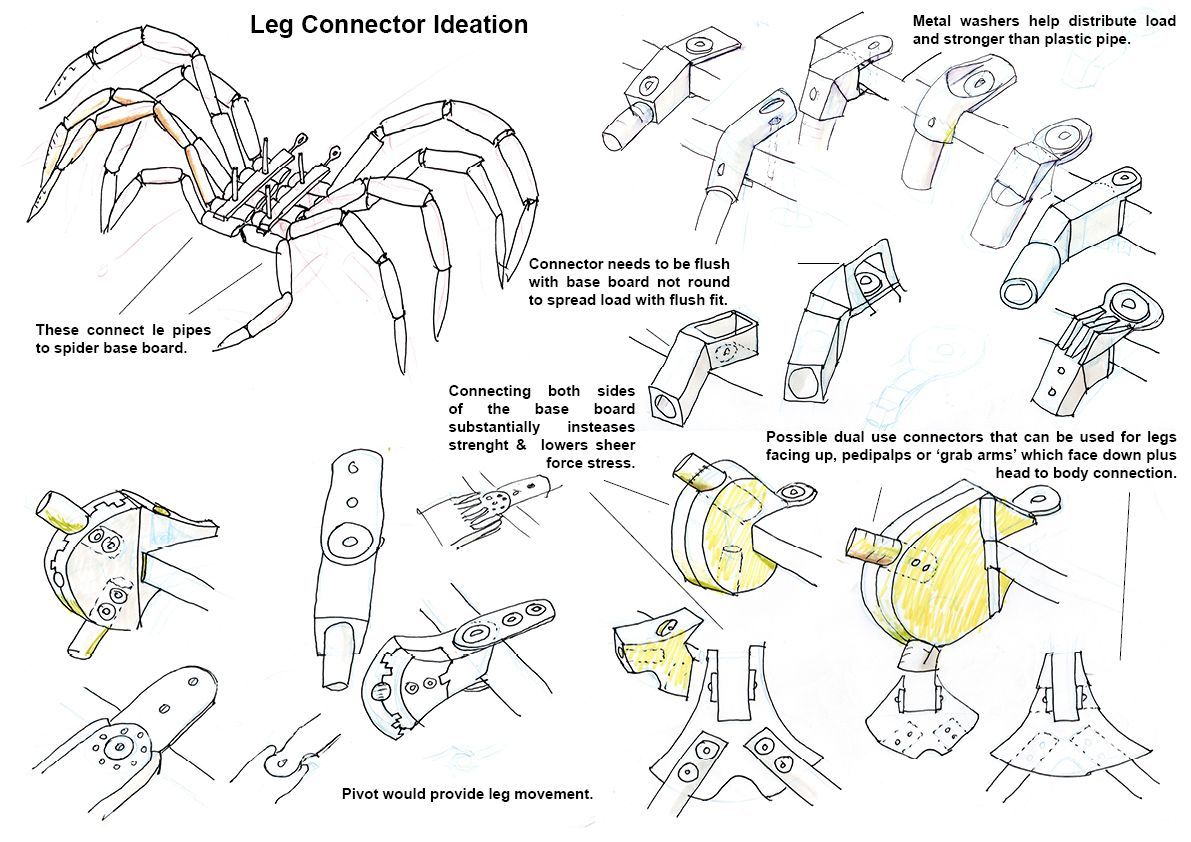
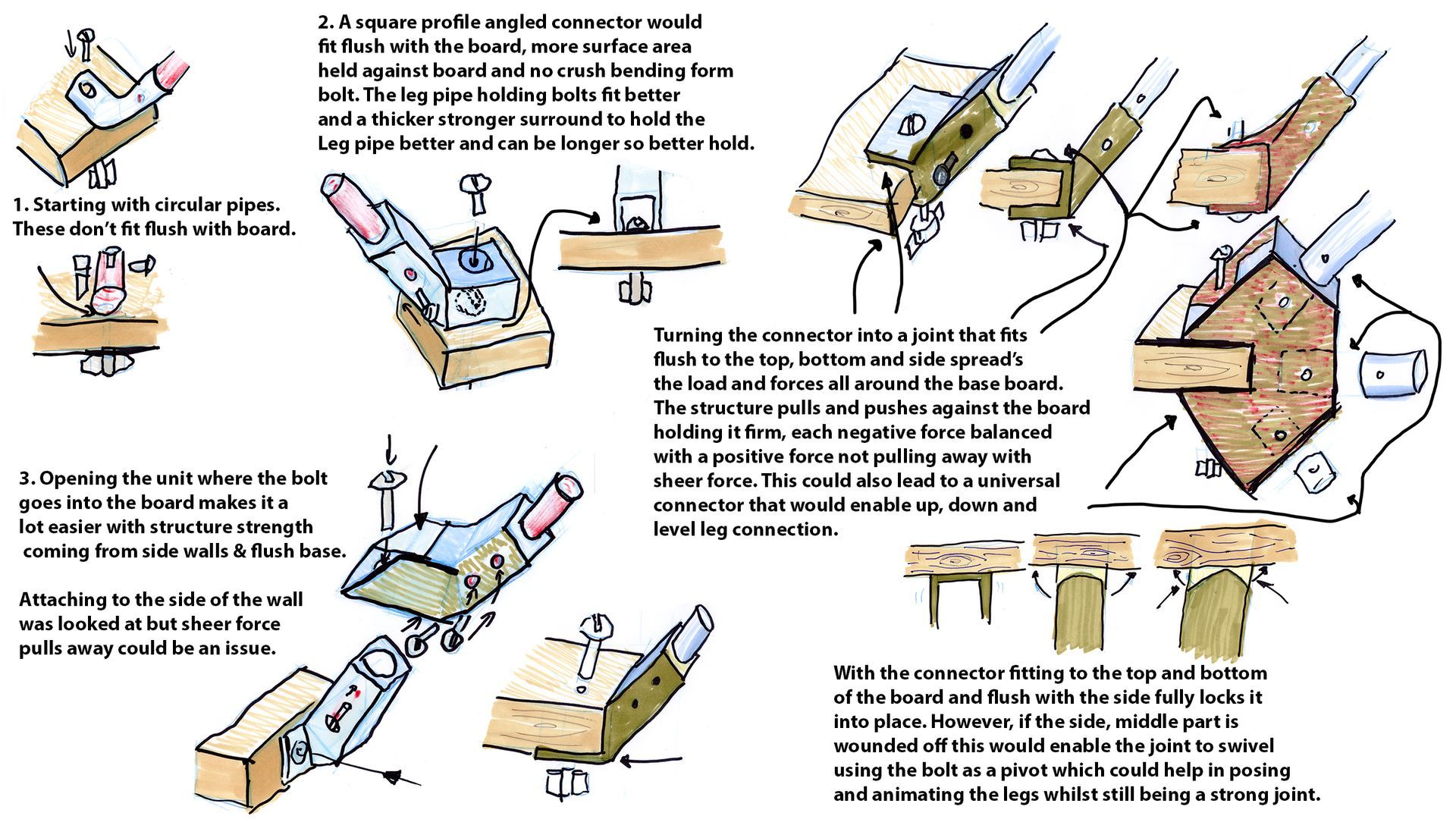
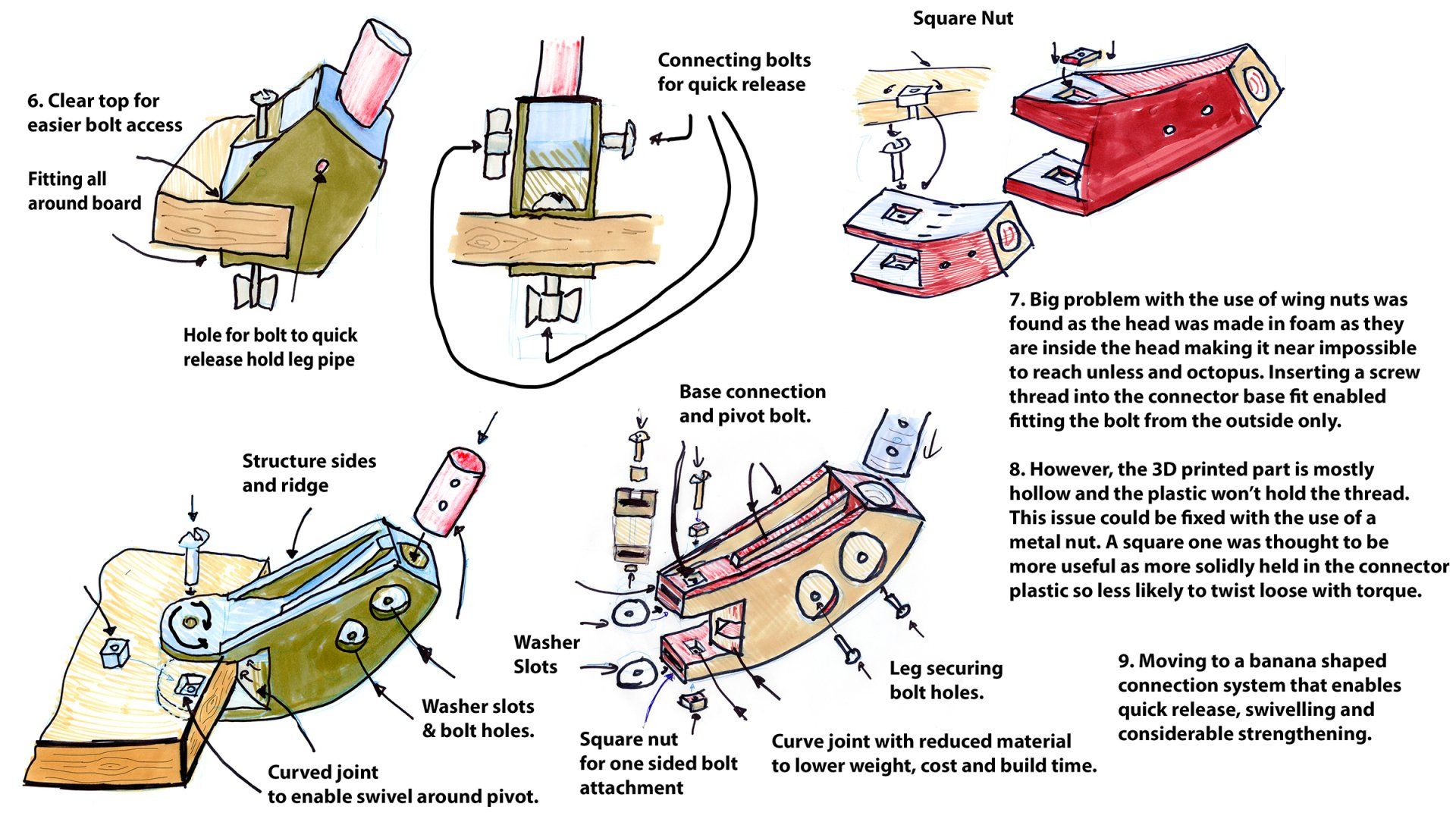
Proving Principle Prototyping
CAD Development
Taking what was learned from the sketch ideation and foam board prototype testing then moved onto CAD development for rapid prototyping on Solidworks to create the first 3d printed prototypes on my Raise 3D N2 3D printer.
A more rounded form was created to look more organic but this did make it harder to hold in place for post - production work in vices.
At least 10 versions were produced.
The first few were primary being tweaked to fit the additional components better like the leg pipes. At first the shaft was too tight then too loose. Similar situation for the metal washer slots and bolt holes.
At first the bolt holes had a screw thread tap designed into the STL files in photoshop. Then with a tapping wrench before What was found was that this took too long for the bolts to be screwed in, too tights and also being a soft PLA plastic very soon wore out within a few insertions.
Thus, the holes were widened to be a 1mm then ½ mm to just let the bolts slip though where they went through the shaft and though half the board holding end before switching the board holding wing nut for an embedded square not to be superglued in place after 3d Printing. The nut enabled fighting enough to hold the connector in place but just loose enough to swivel to pose a leg
The square nut being chosen over hexagonal as less likely to work loose through torque.
Other iterations pushed the shaft further out and at a more acute angle to the legs would be more vertical.
More to try and minimise the material to lower cost and speed up the 3D printing process.
The swivel curve was made more triangular, sides rounded off the increase the swivel range , slots added to pivot to reduce material & build time.
It needs 1-2mm wire reinforcement running from the washer slot base board attachments to the other side to deal with sheer forced due to extra spider weight in furture developments. This is also due to the 3D printing process in layers. Due to all the over hangs & gaps this can only be done vertically which means these are weak right at the angle of the sheer forces which can snap the base board joins off. This would be glued in place.
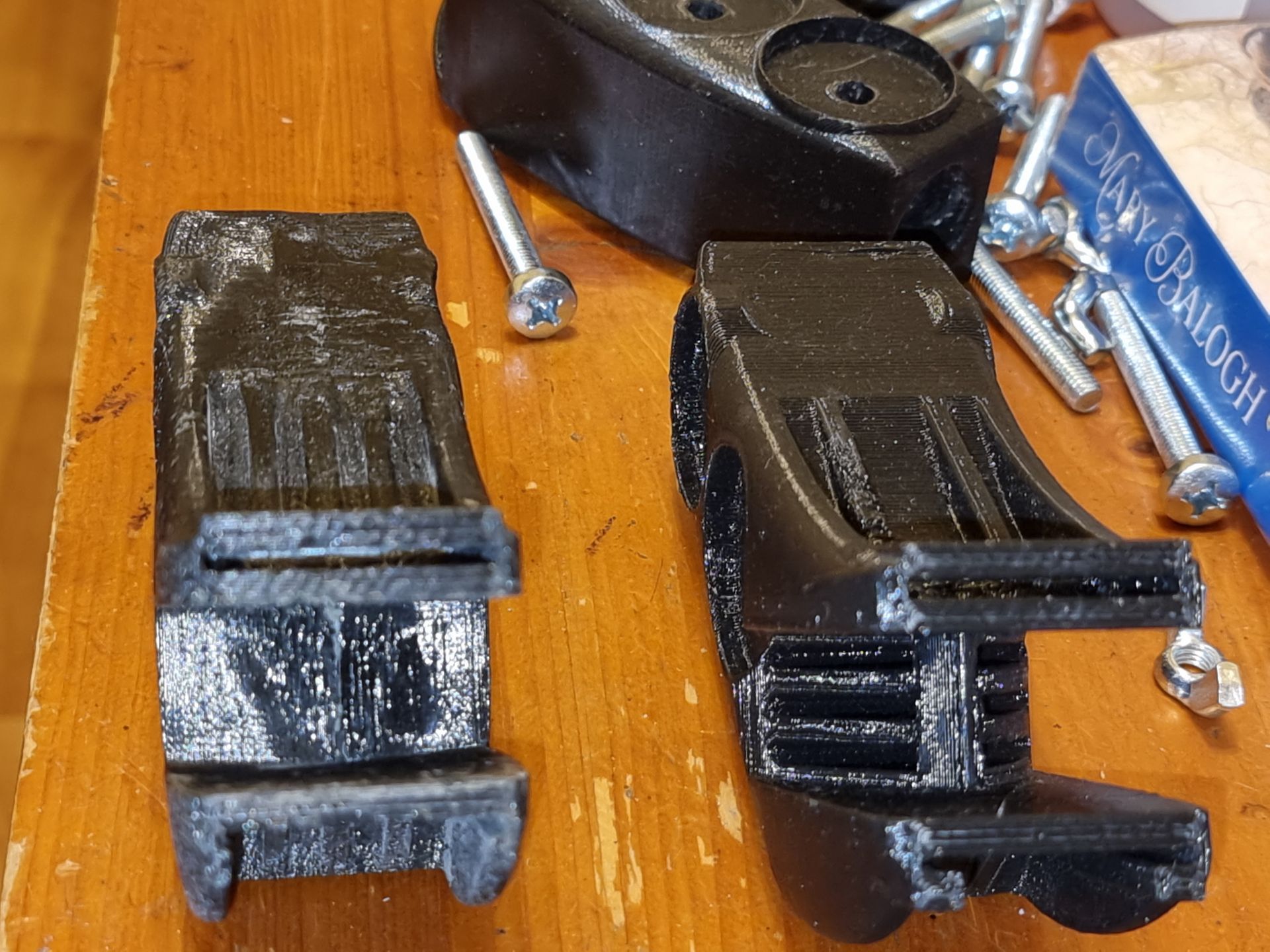
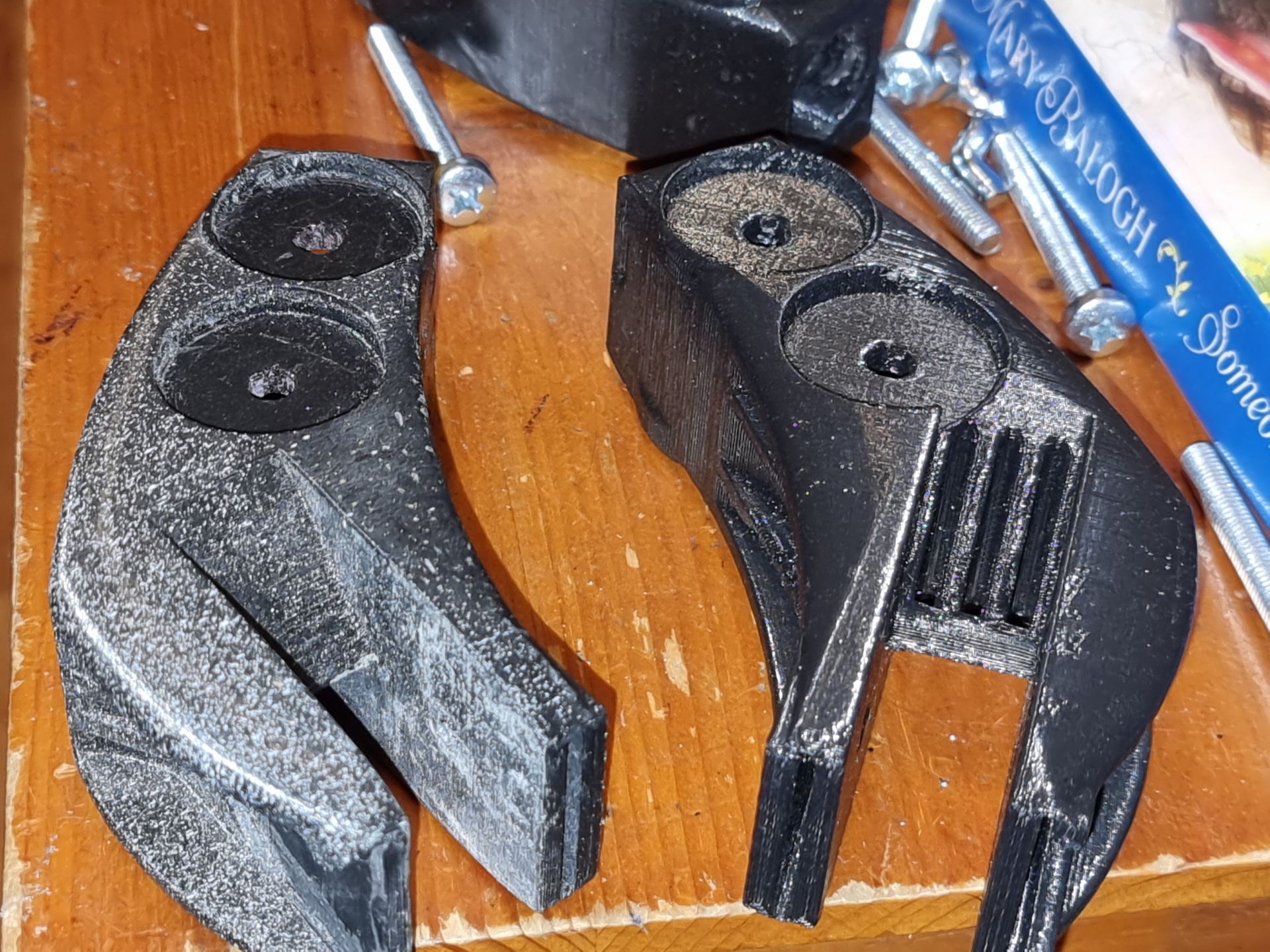
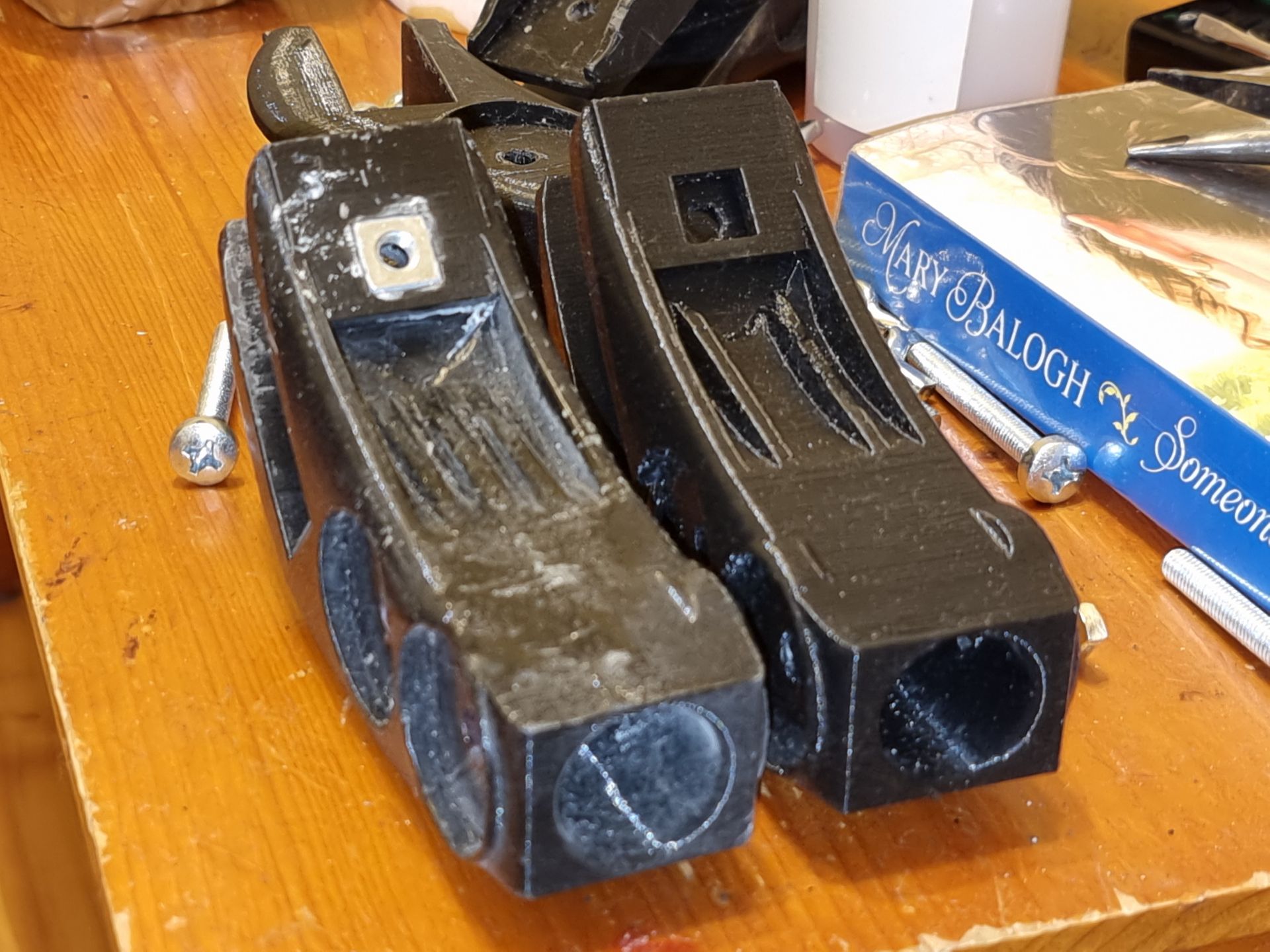
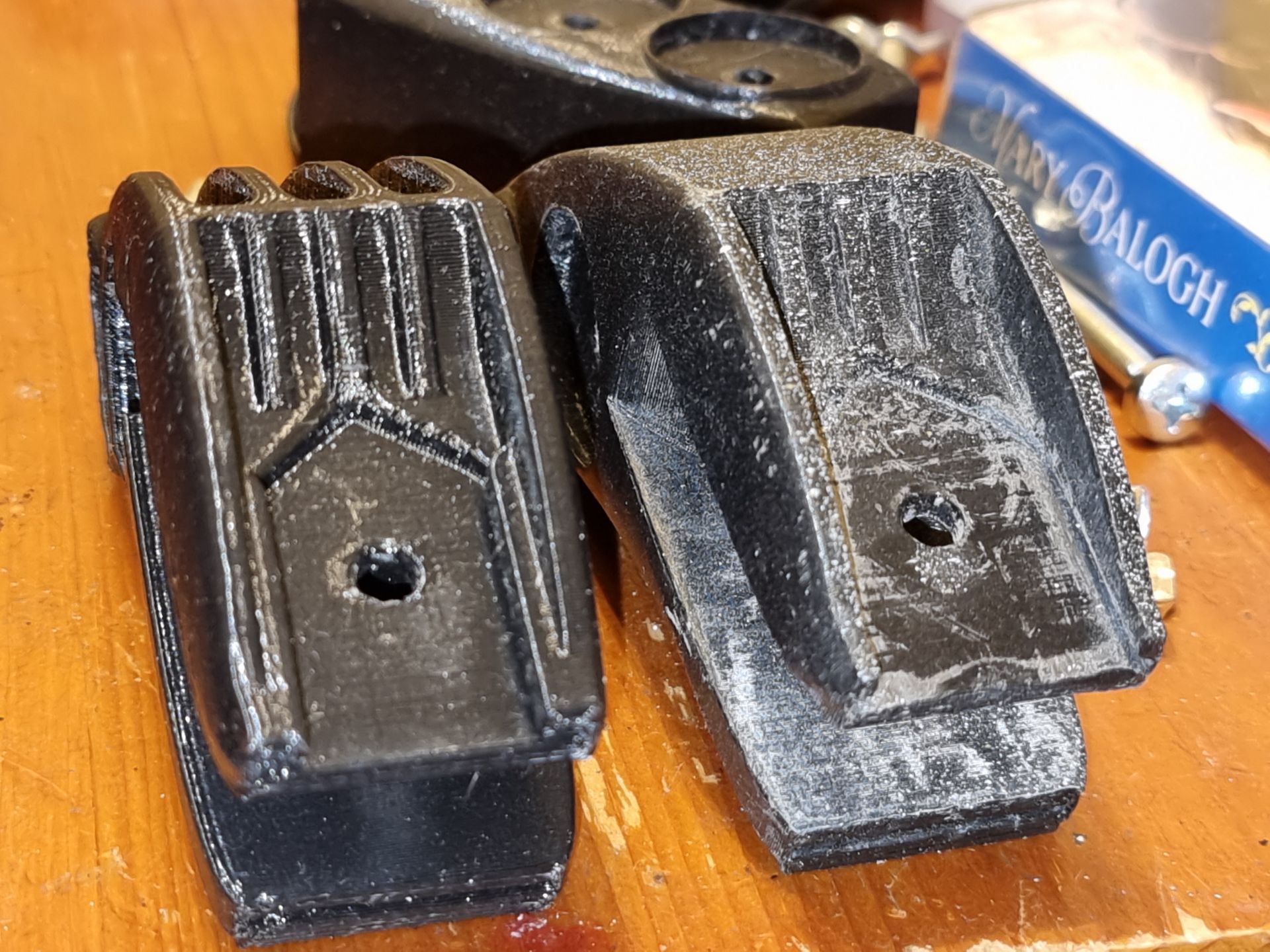
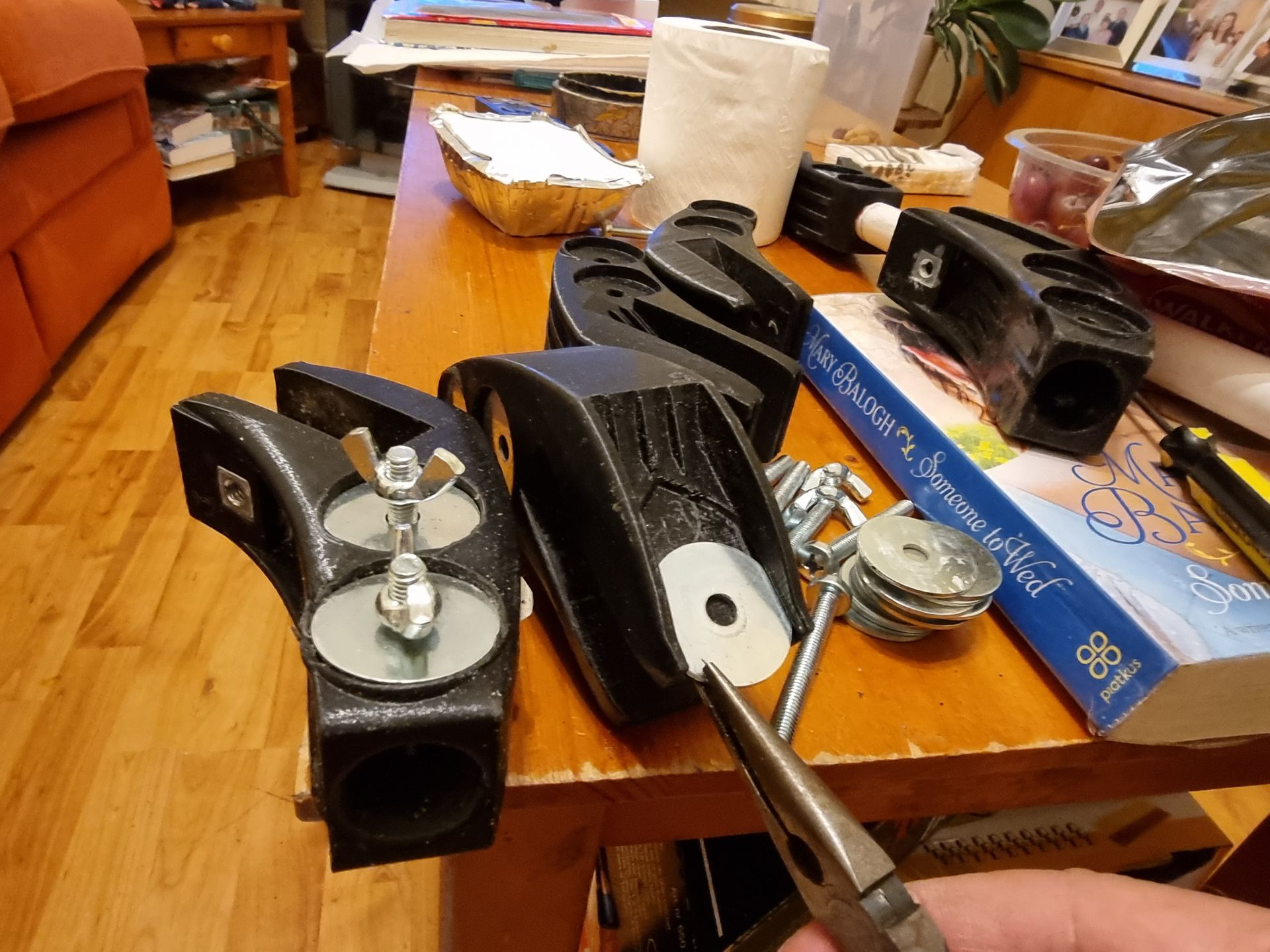
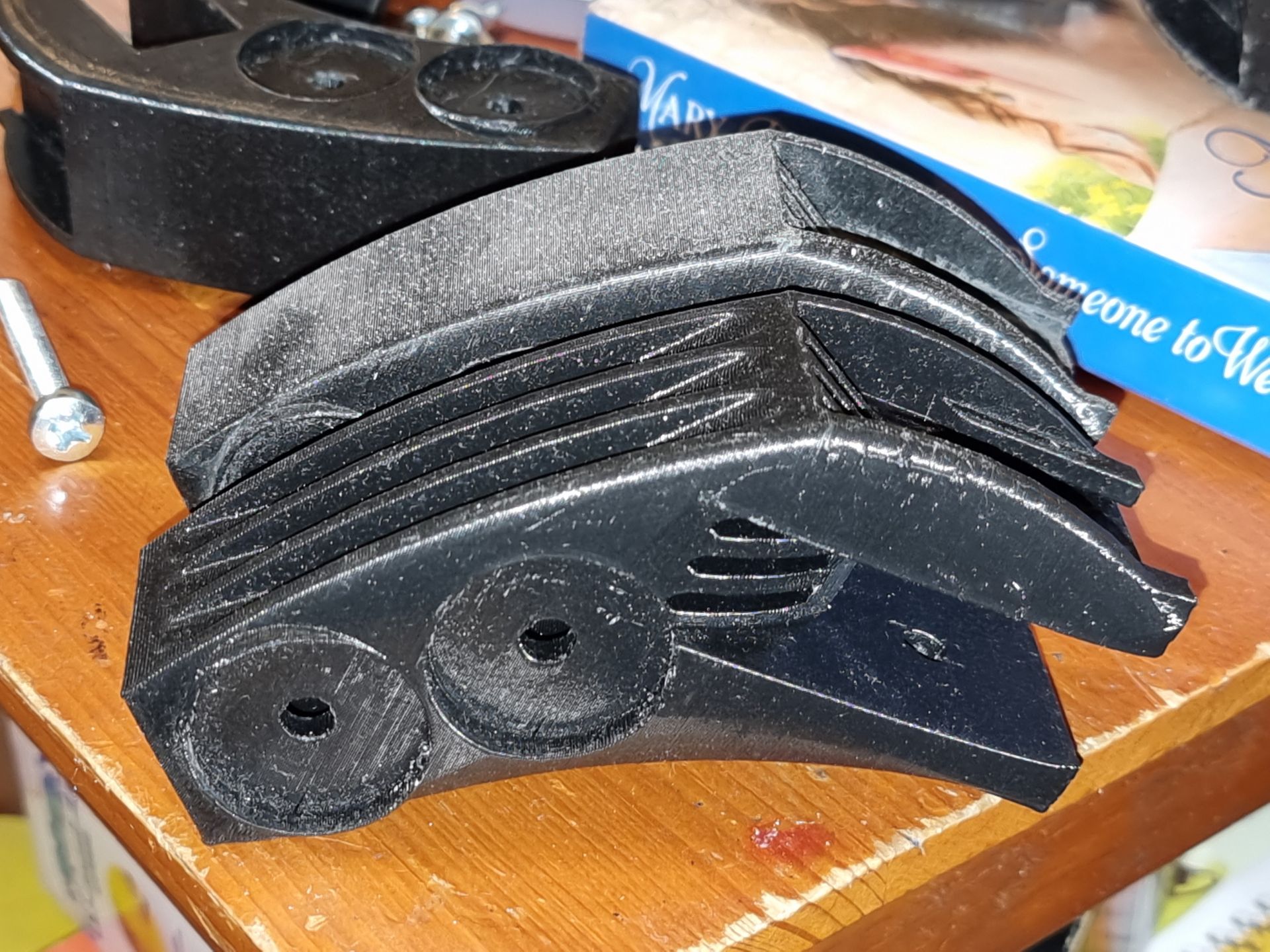
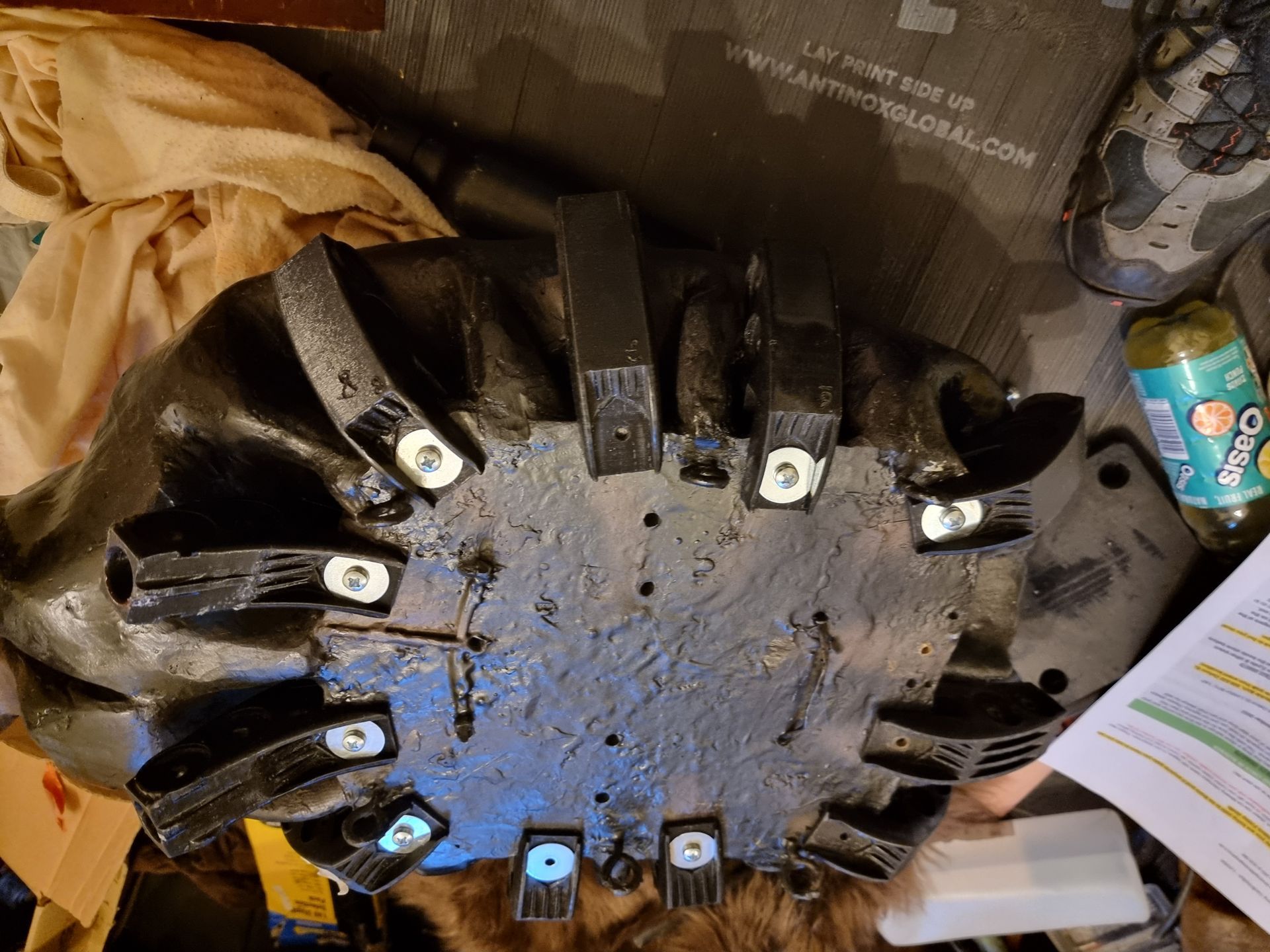