Strengthened Strap Film Bag
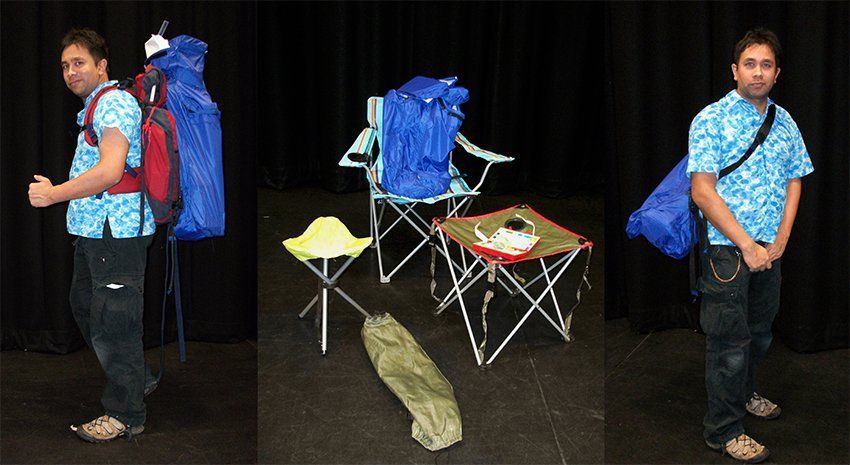
Intro
This bag was a personal project. I work a lot on films as a background actor also known as a film extra or supporting artist and this involves waiting around for hours on end. It helps to bring some comfort items to help pass the time comfortably. More importantly there is the requirement to bring several clothing changes to fit the role or multiple roles I will be playing. Thus a customised bag would help that was also light and strong.
The bag itself if not so original or good in the aesthetics department, however it was a good test bed for a theory I had on how to make far tougher strap connections to bags. This was to counter the common problem I have had with bag straps peeling off over time due to sheer forces breaking the threads.
The bag itself if not so original or good in the aesthetics department, however it was a good test bed for a theory I had on how to make far tougher strap connections to bags. This was to counter the common problem I have had with bag straps peeling off over time due to sheer forces breaking the threads.
Problem to Address
Most rucksack straps come off at the joint in the (L) shape where a flap is from the strap is connected to the bag.
The theory is that if you remove this by making the connection more of a (T) shape this spreads the pull forces over the entire surface of the flaps in both directions, not a small a small stress point likely to fail.
The theory is that if you remove this by making the connection more of a (T) shape this spreads the pull forces over the entire surface of the flaps in both directions, not a small a small stress point likely to fail.
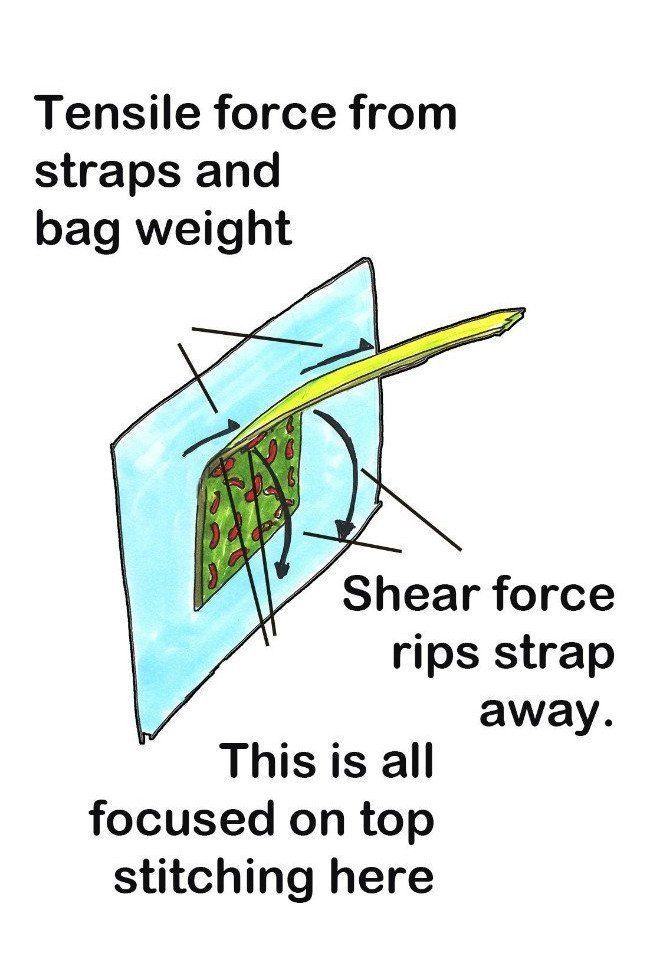
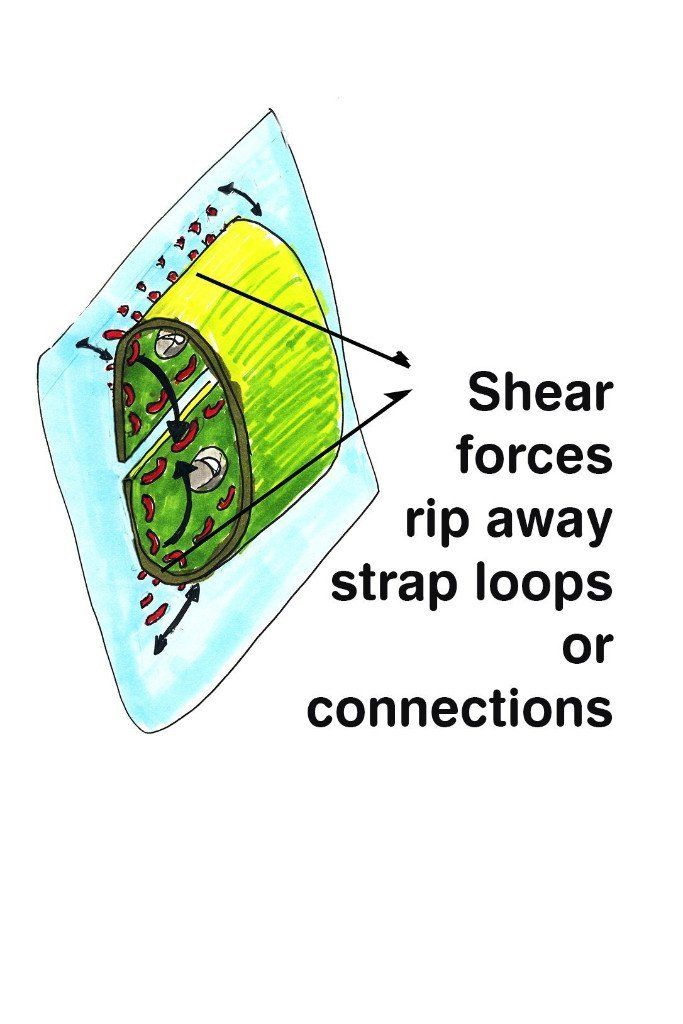
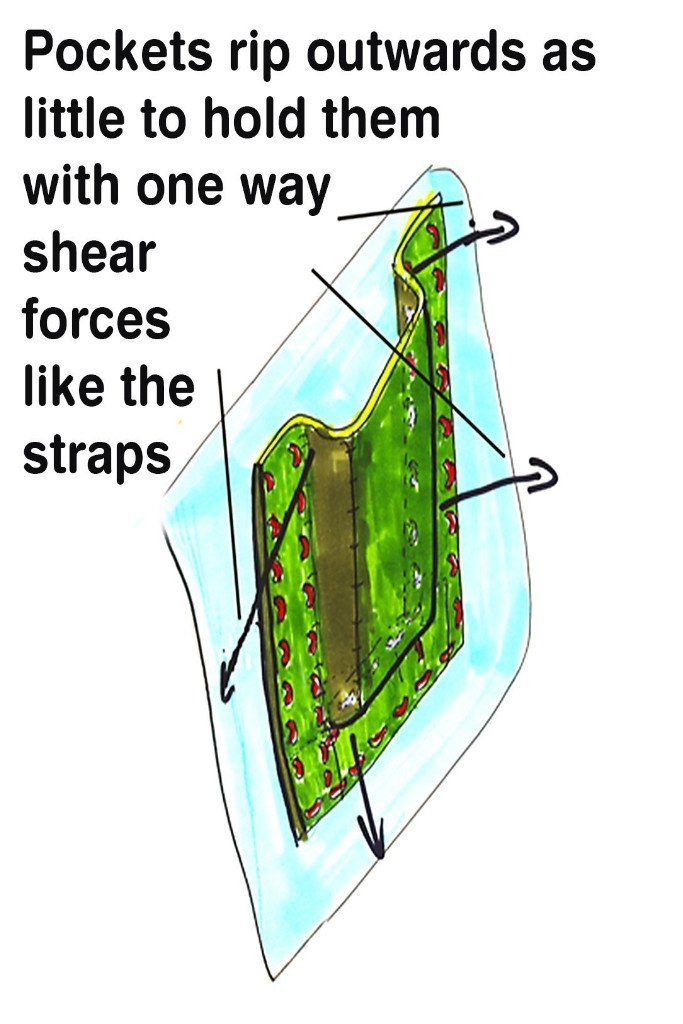
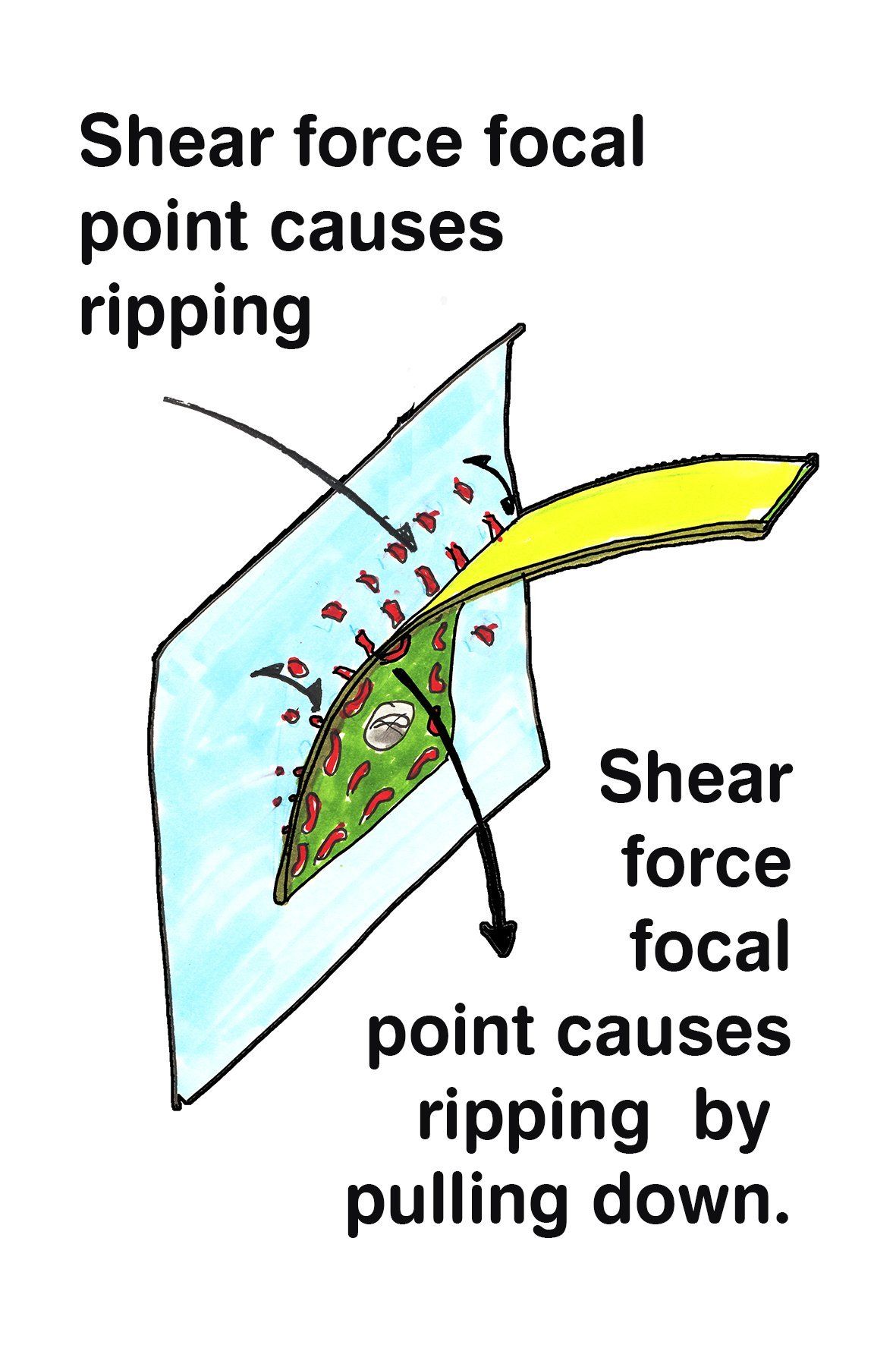
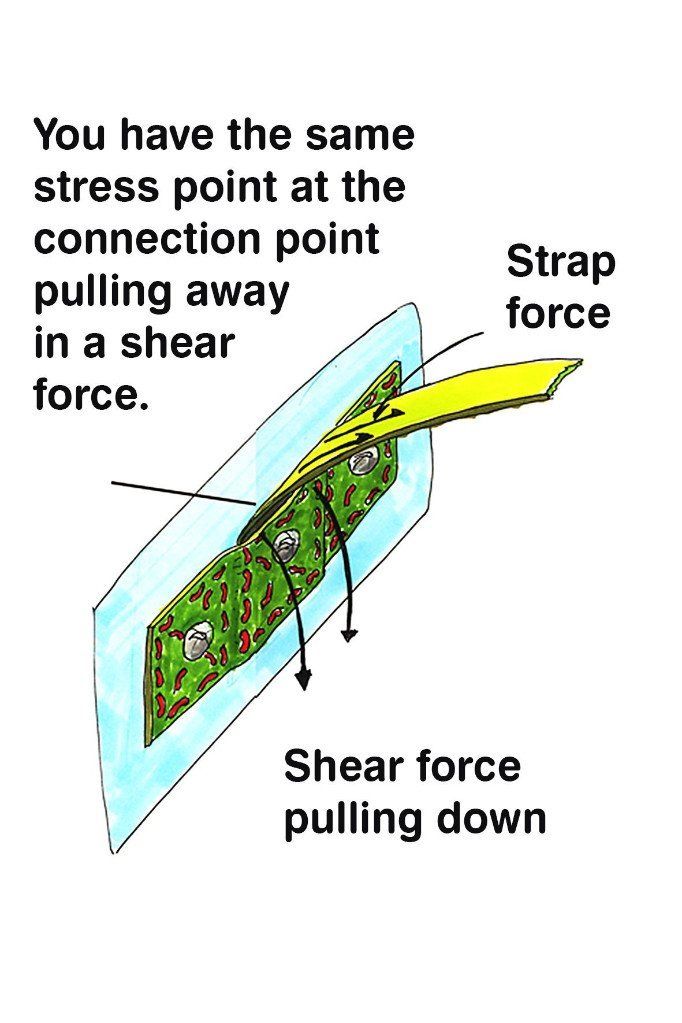
Theoretical Solution - From L-Stitching to T-Stitching Patterns
The concept for this came during merchandising work. Here as I had car I had to work out ways of repacking POS (Point of Sale) promotional items such as this FSDU (Free Standing Display Unit - or the promotional cardboard towers they stick new items in the shop in to help sales), so I could transport to location on public transport.
Necessity being the mother of invention, I used Duct tape strapping systems to make it more comfortable and easier to carry. The tape pulls away from the box much easier than a sewn on strap on a backpack but the principles why are the same in terms of shear forces causing peel off as all the forces are applies to a small line of adhesion or sewing causing a stress point to fracture.
Necessity being the mother of invention, I used Duct tape strapping systems to make it more comfortable and easier to carry. The tape pulls away from the box much easier than a sewn on strap on a backpack but the principles why are the same in terms of shear forces causing peel off as all the forces are applies to a small line of adhesion or sewing causing a stress point to fracture.
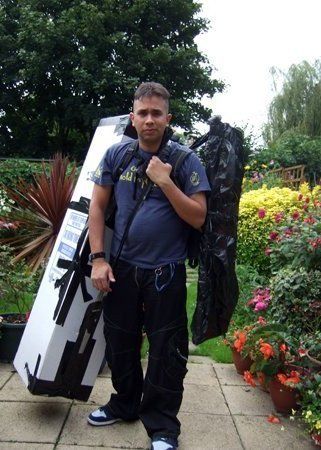
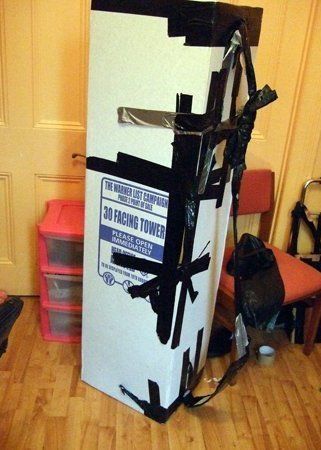
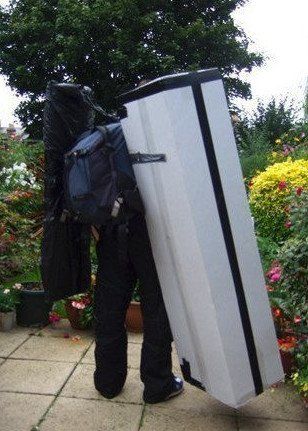
PPP Proving Principle Prototyping
My theory was that if you remove this by making the connection more of a (T) shape this spreads the pull forces over the entire surface of the flaps in both directions, not a small a small stress line likely to fail as can be seen above.
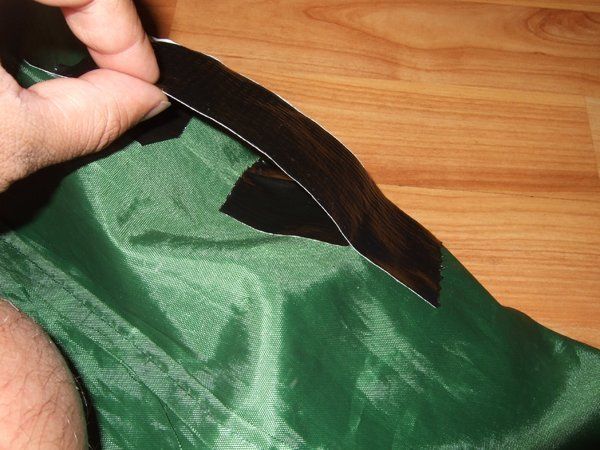
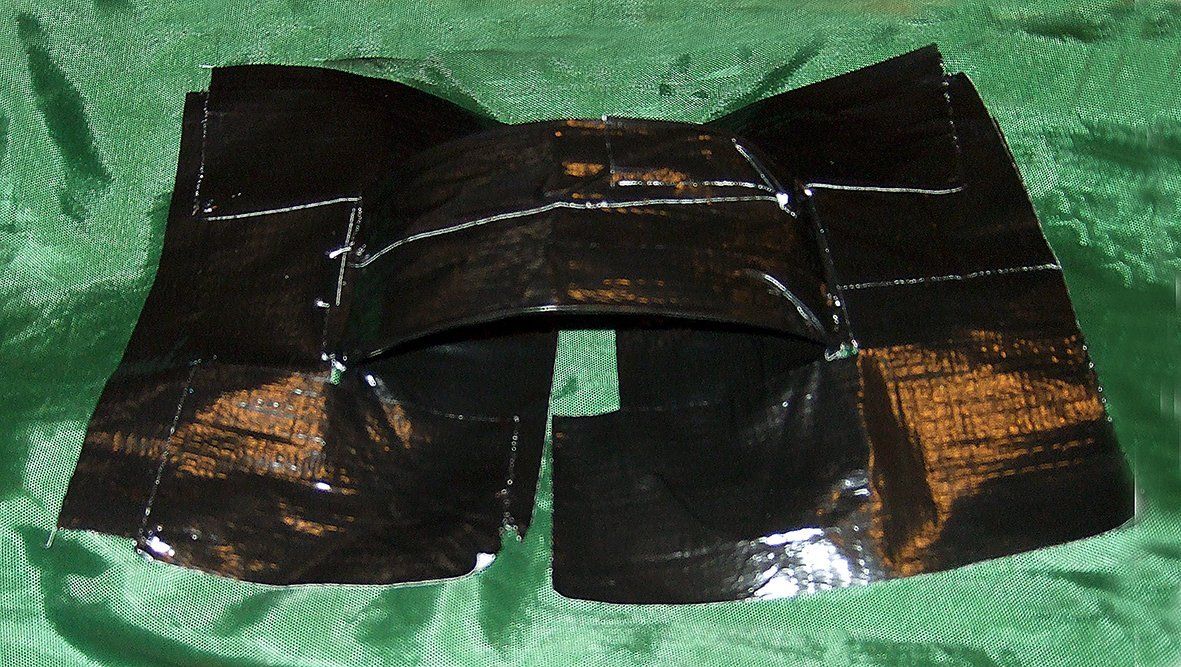
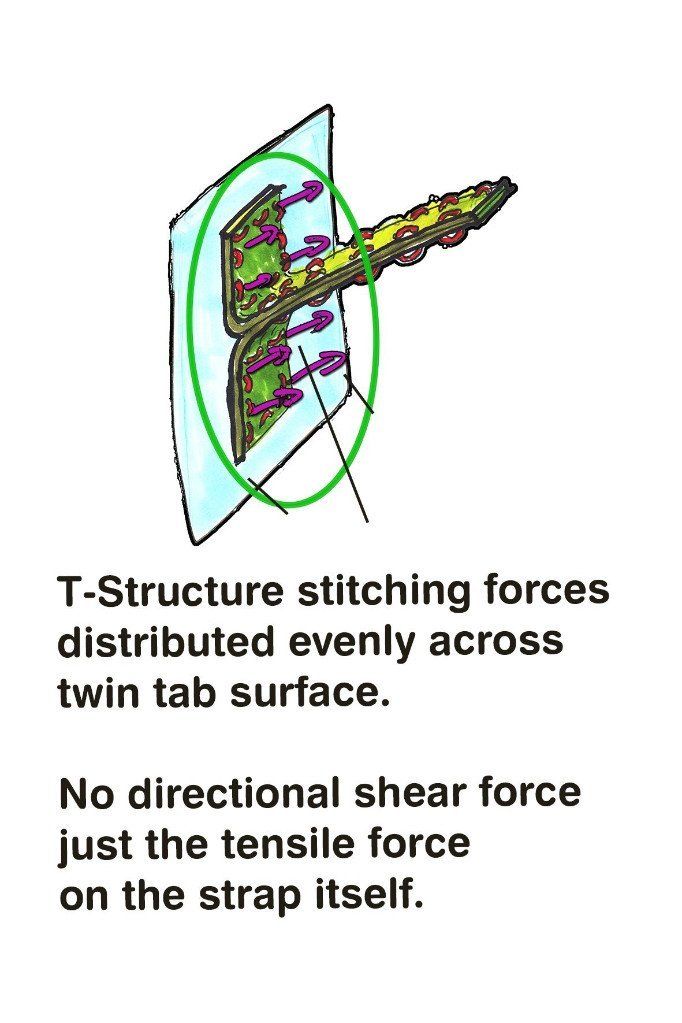
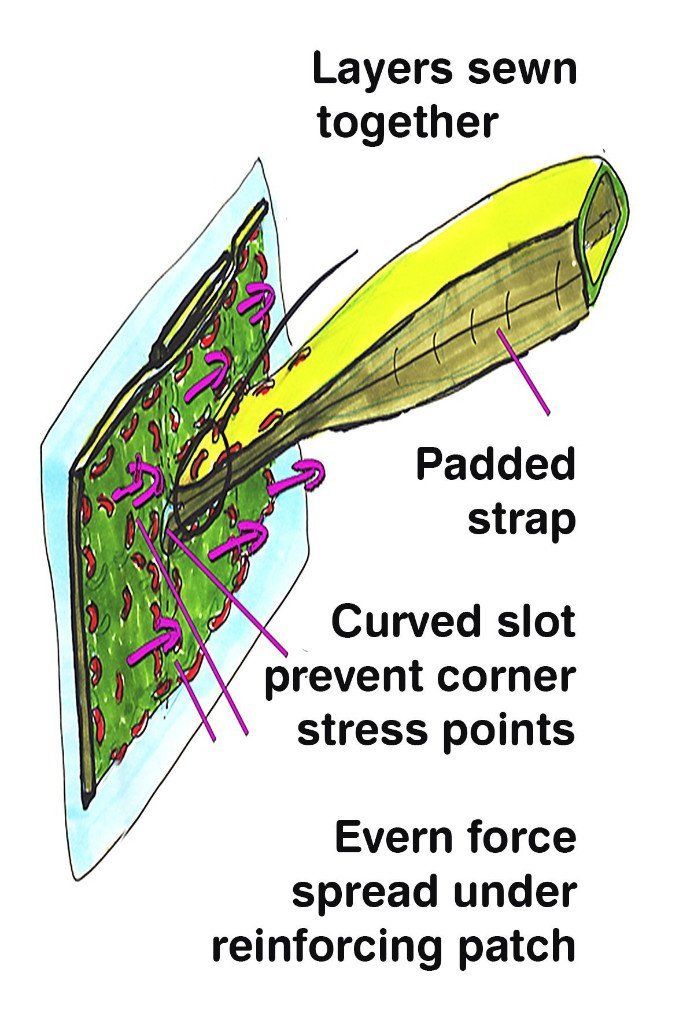
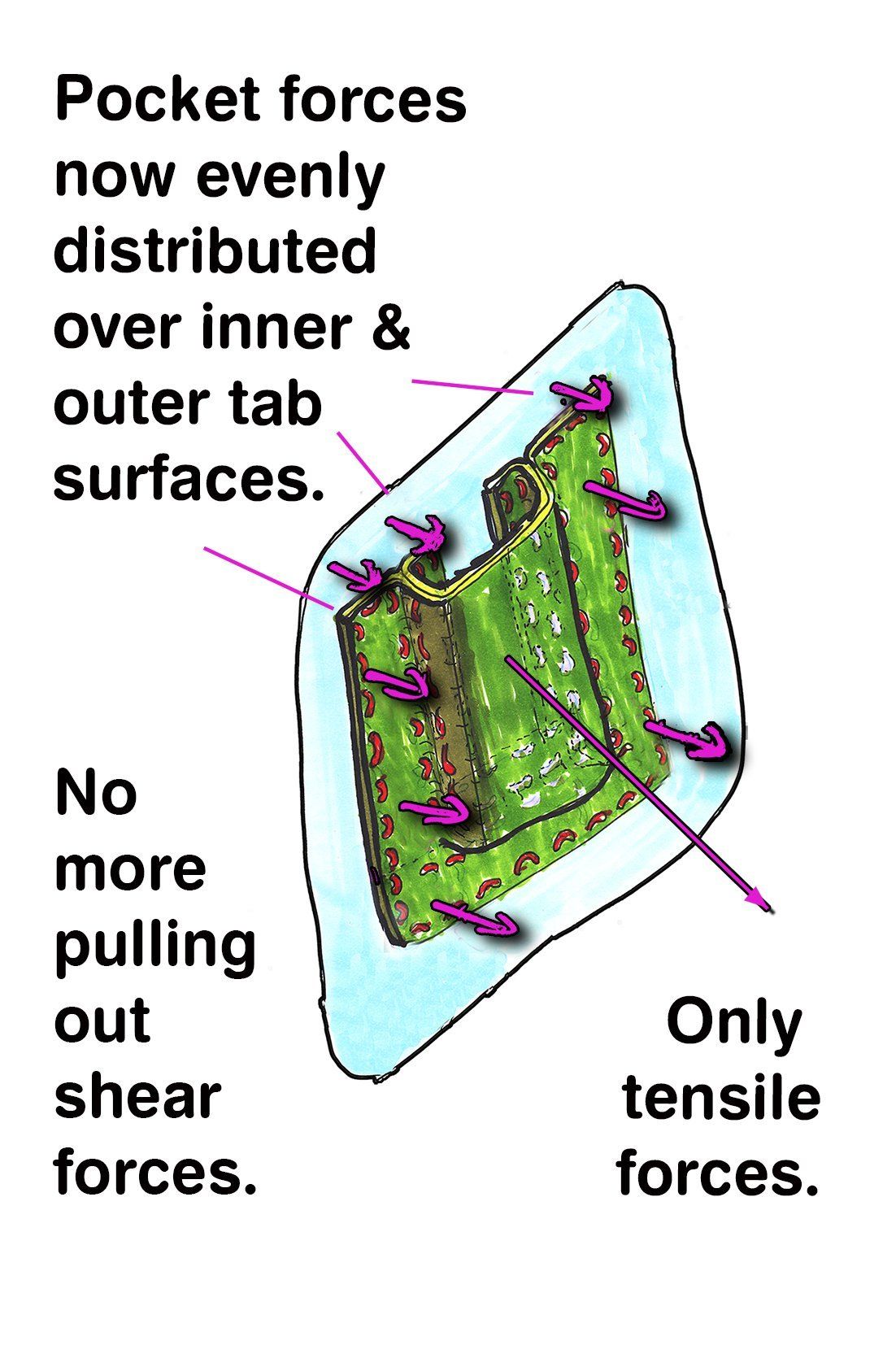
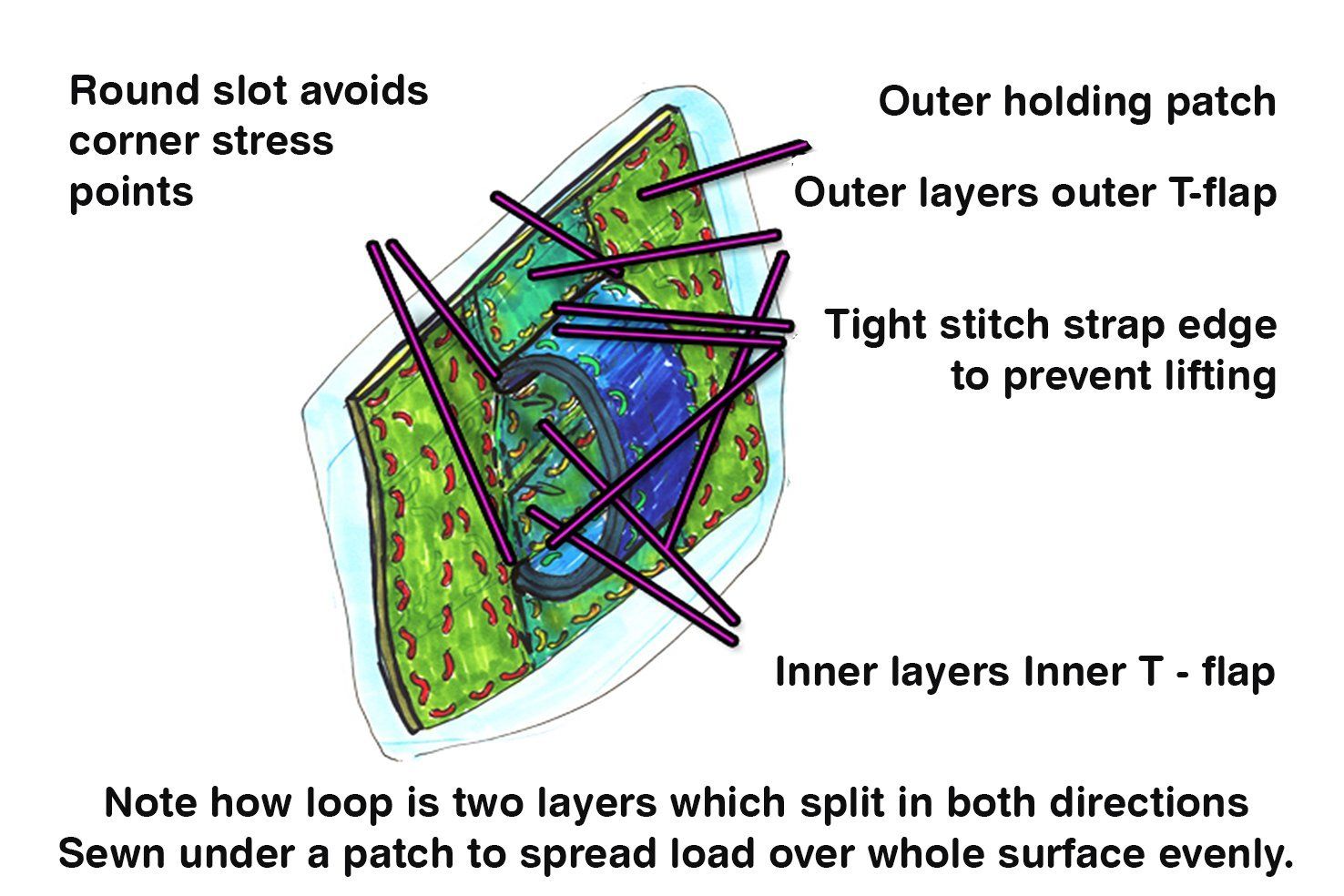
Product Design Specifications
The bag needs to be able to comfortably hold:
- Folding Table.
- Strip adapter.
- A fold up chair.
- Extension lead.
- Phone charger.
- Folding mini stool.
- Note paper and pens.
- A variety of clothing options.
- Games bag with poker chips, Connect 4, books.
- Have pockets.
- Sealable and rain proof.
- Be lightweight and strong.
- Have adjustable strapping.
- Worn comfortably alongside a rucksack.
- Sealed ends to the straps to stop fraying.
- Have easy entrance for fast insertion of fold up chair etc.
- Some form of soft structure that holds the bag open but can be folded flat.
Sketch Concept Ideation
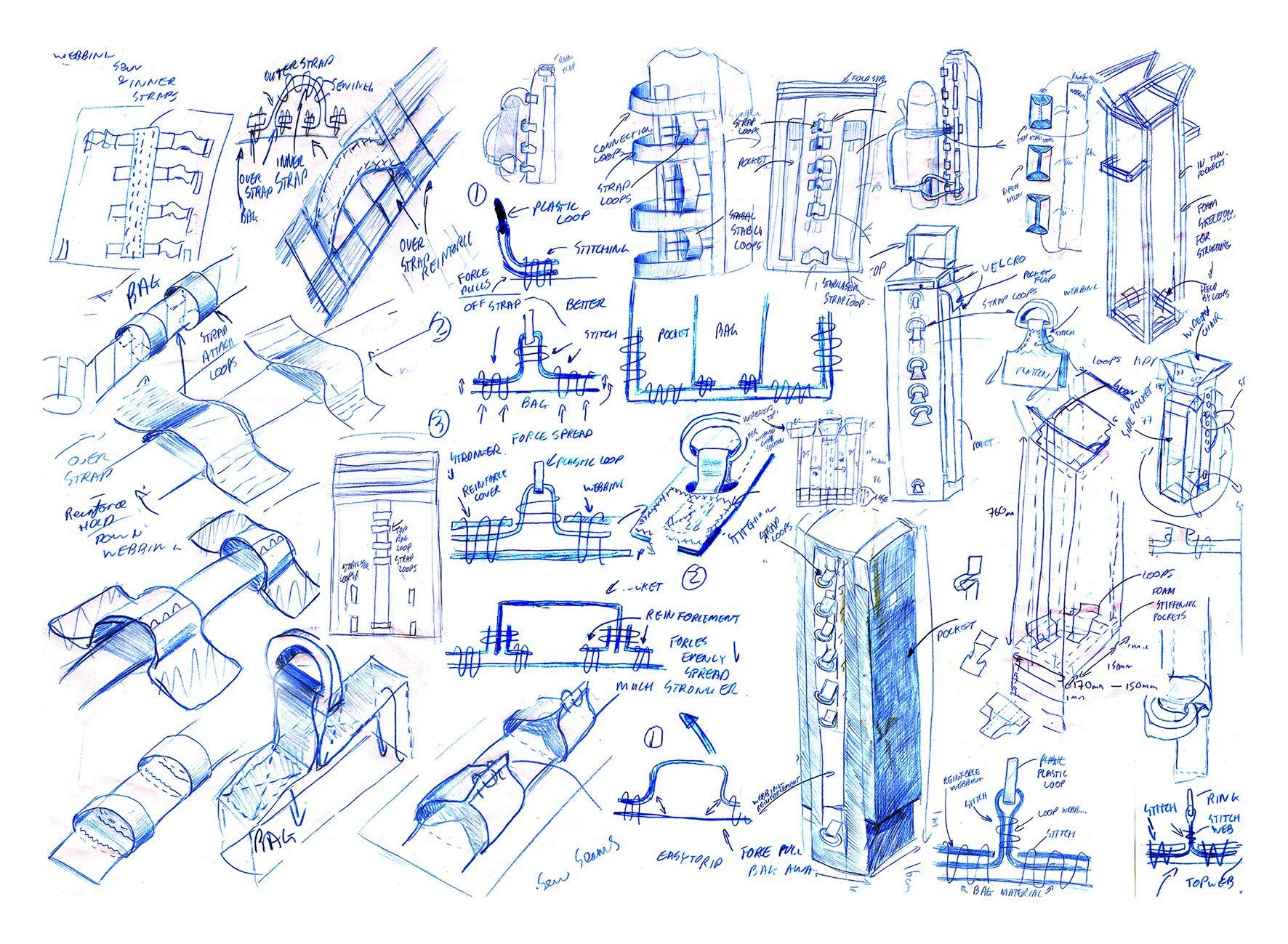
Easy Opening Prototyping
The bag that the folding chair came in was often awkward to insert the chair into with no structure to hold it open. This slows things down often when I had to rapidly pack to move location. Having a system to funnel the opening helps achieve this along with an overlapping top.
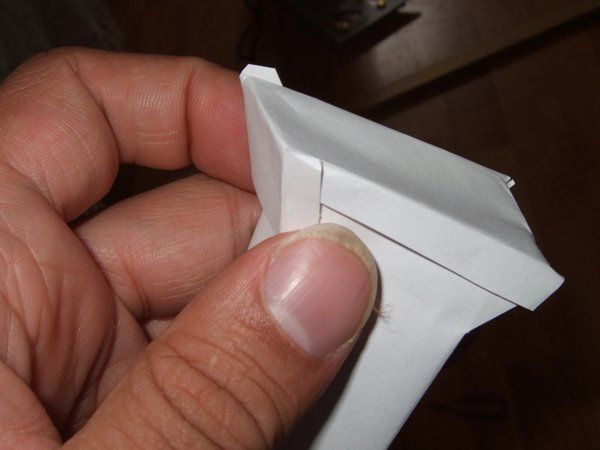
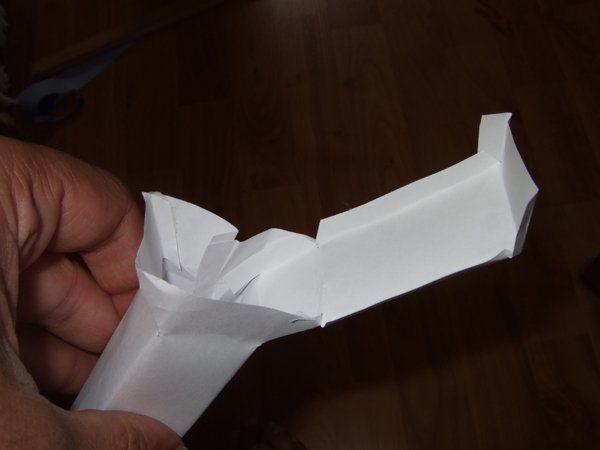
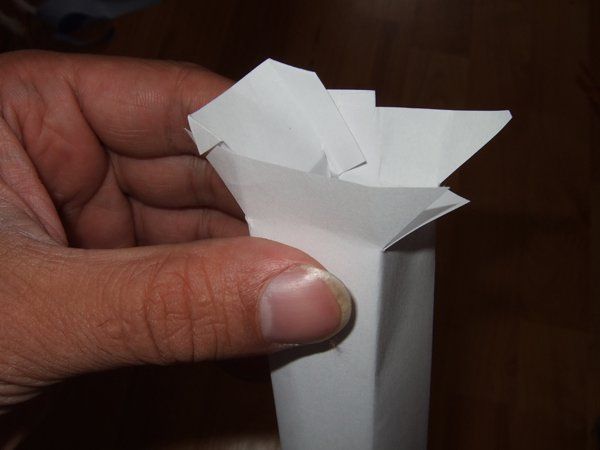
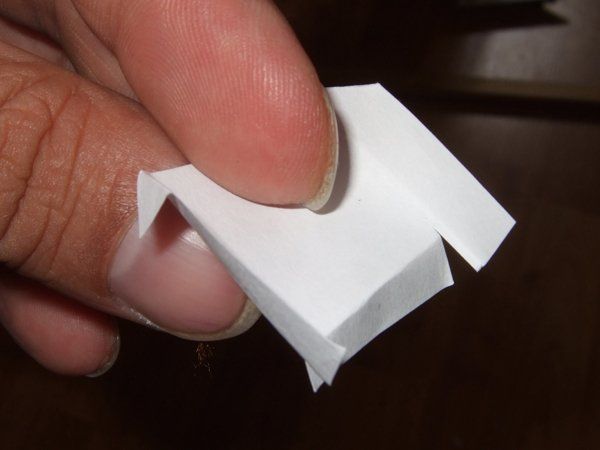
Construction of First Working Prototype and Current Bag
The bag that the folding chair came in was often awkward to insert the chair into with no structure to hold it open. This slows things down often when I had to rapidly pack to move location. Having a system to funnel the opening helps achieve this along with an overlapping top.
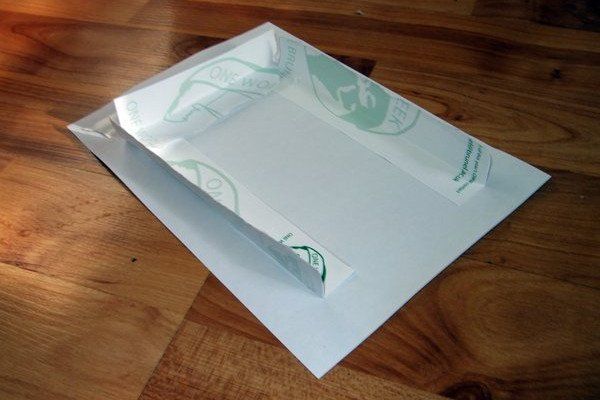
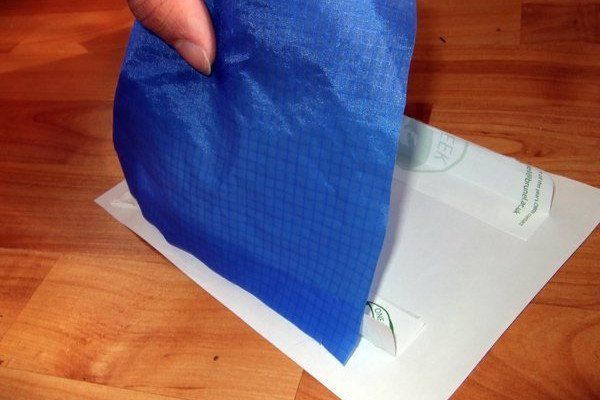
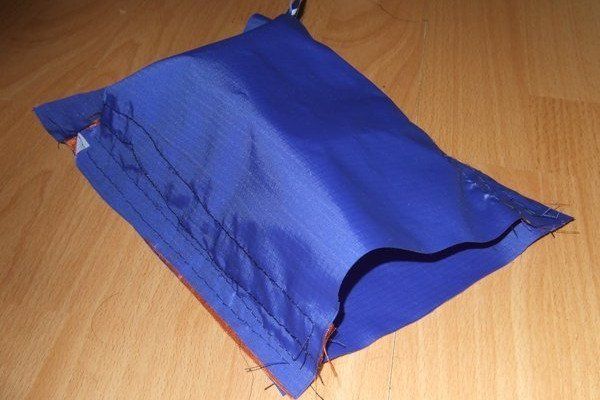
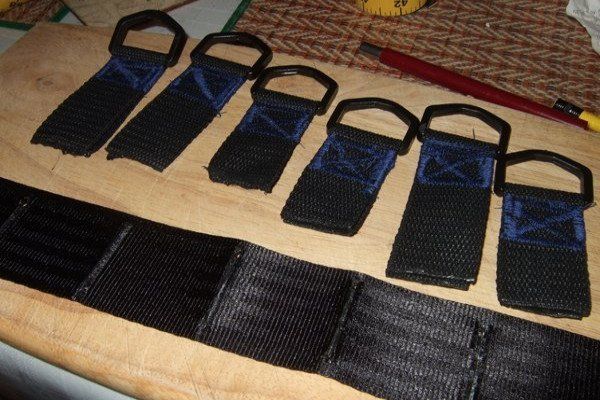
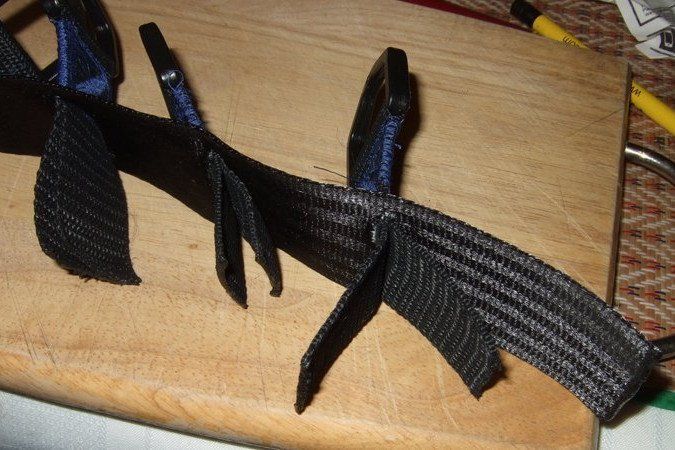
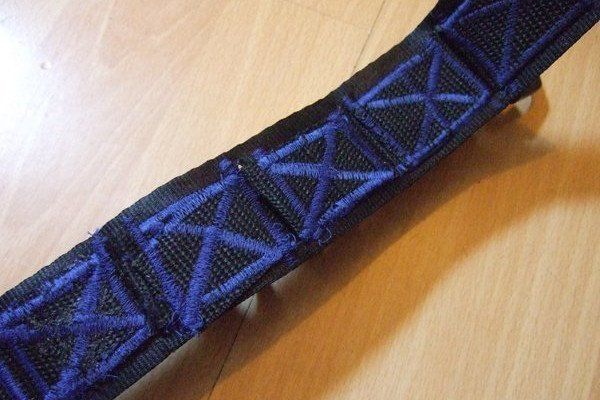
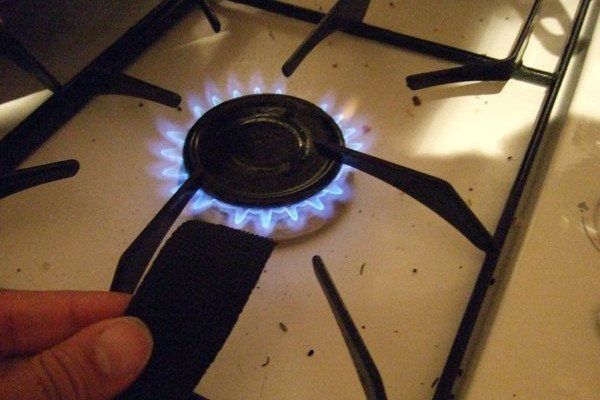
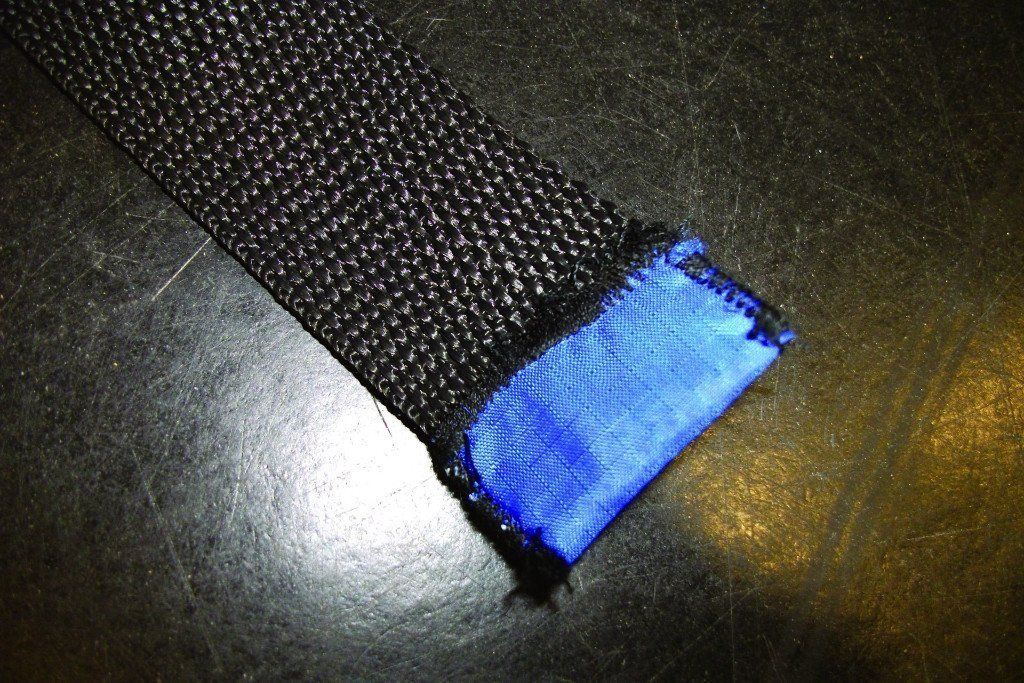
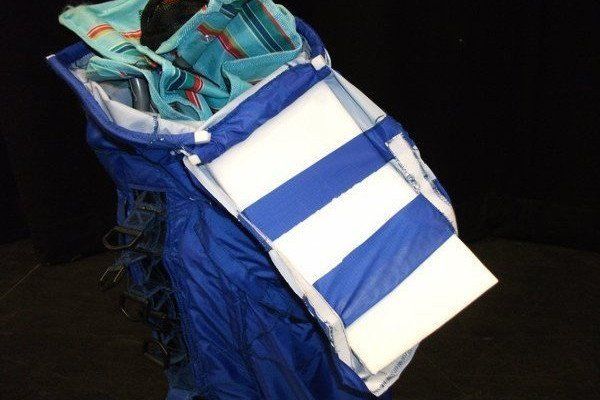
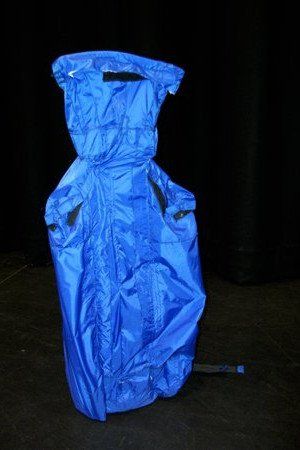
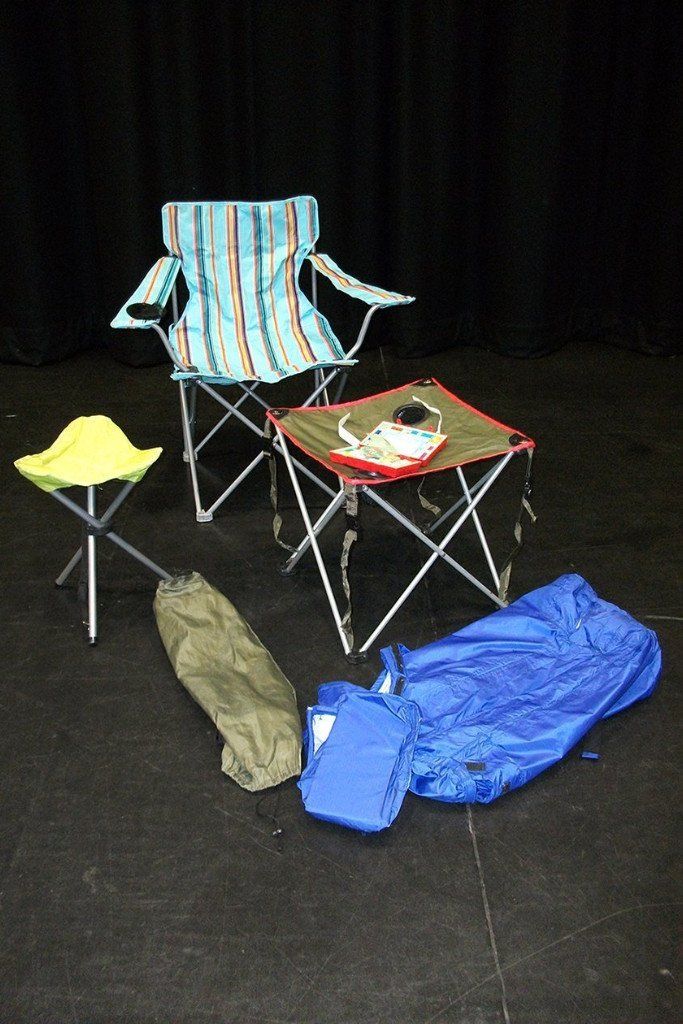
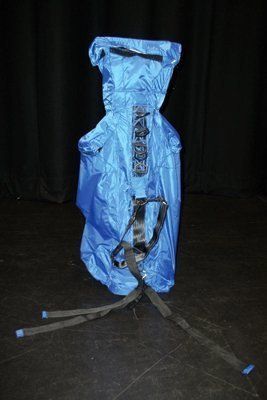
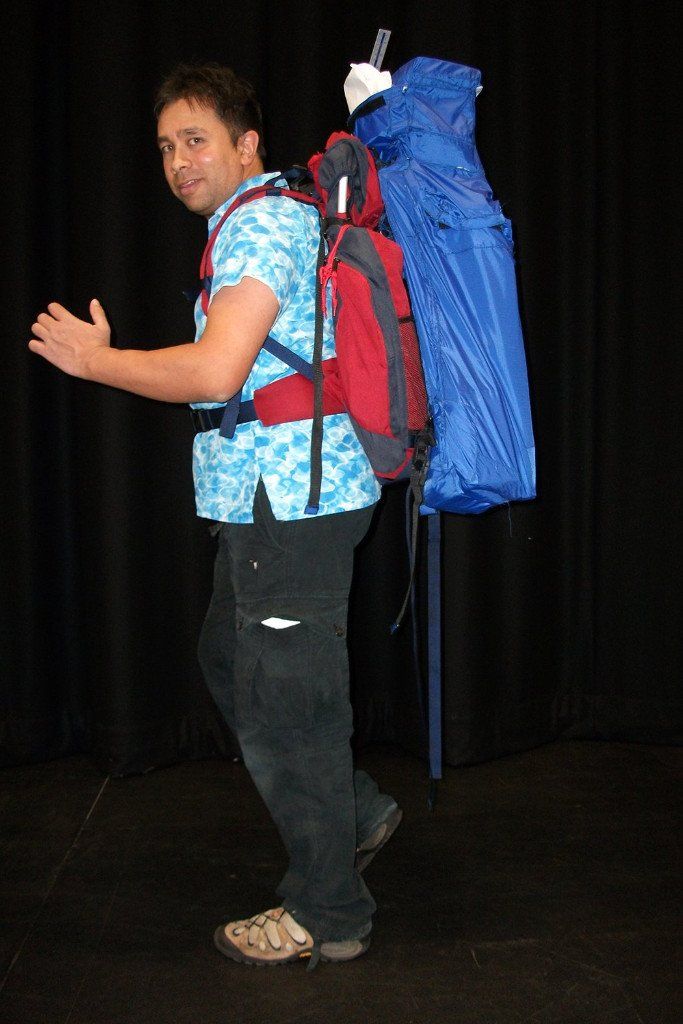
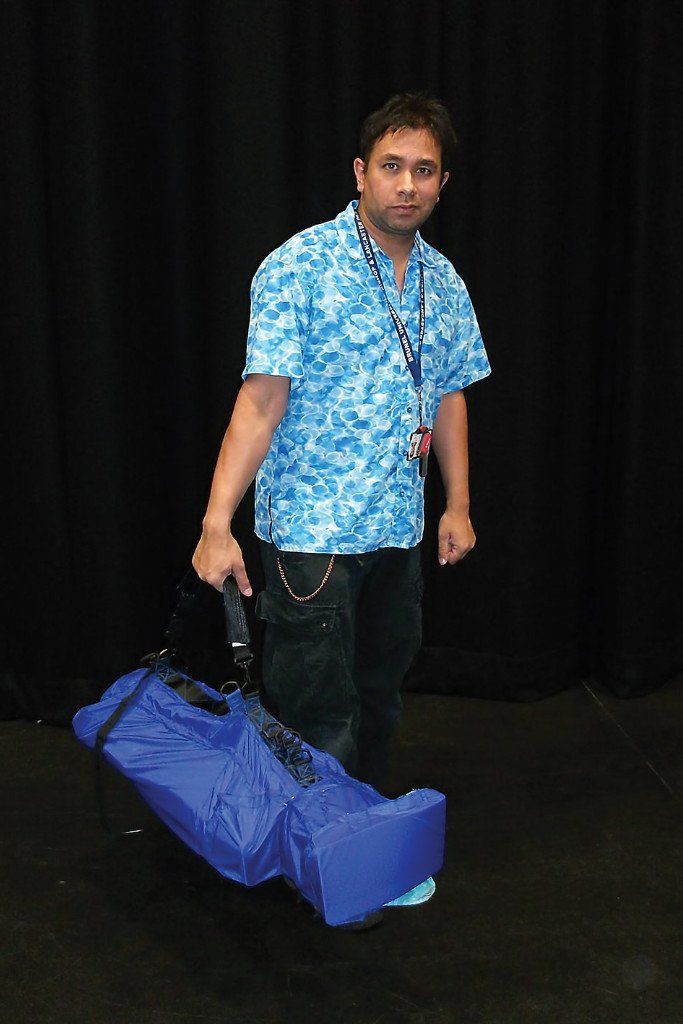
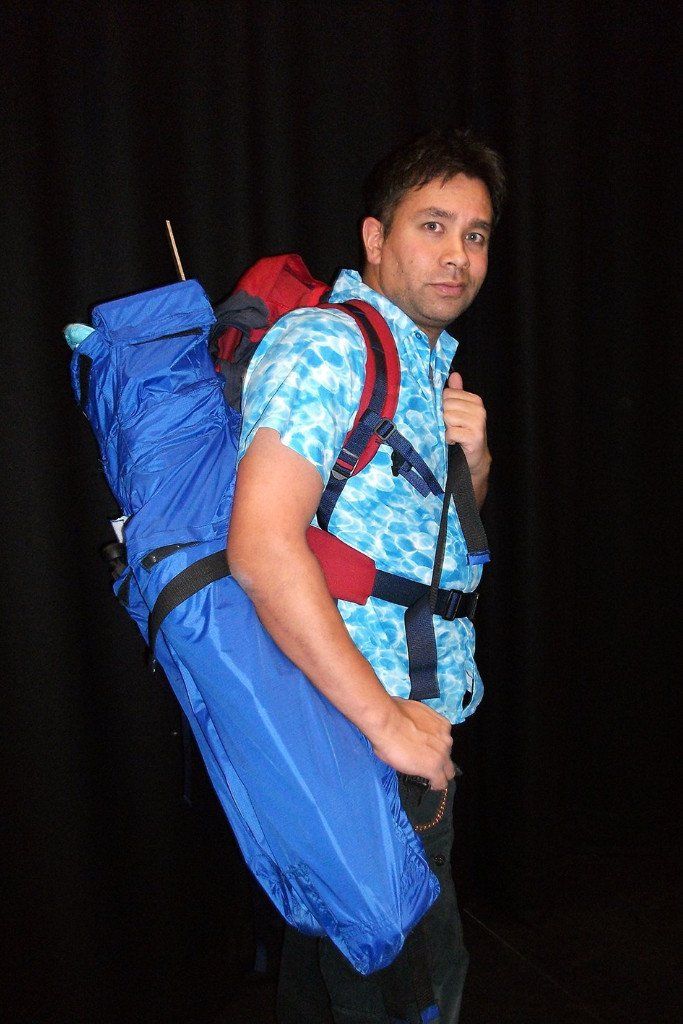
- The materials of choice were webbing like on seatbelts and double layer Ripstop Nylon. A paper former was used to help form the pockets.
- A choice of connection points was added with D rings tightly sewn together with folded webbing leave the reap points to be split for bi direction sewing connections. This allows for different configurations.
- This was fed though other webbing slots with rounded ends then split and sewn into place. Triangular sewing patterns give strength.
- The webbing ends were heat sealed and taped over.
- Plastazote foam was used to form a flexible skeleton structure much like in a shark.